According to the World Health Organization (WHO), ambient air pollution is responsible for approximately 7 million deaths globally each year, highlighting the severe impact of poor air quality on health. Furthermore, the United Nations Environment Programme (UNEP) reports that air pollution contributes to a considerable number of deaths, with harmful particulates and gases causing diseases such as asthma, lung cancer, and heart disease.
In industrial settings, inadequate air monitoring and failure to maintain air quality standards can result in severe health consequences for workers. This highlights not only the demand for advanced monitoring solutions but also the critical need for maintaining these systems to protect health and comply with legal standards.
Navigating OSHA Requirements for Air Monitoring Equipment
To ensure compliance with OSHA's stringent requirements for air monitoring equipment, particularly Direct-Reading Portable Gas Monitors (DRPGMs), adherence to specific protocols is crucial:
- Daily Calibration and Testing: OSHA mandates a bump test or calibration check before each use to ensure accurate detection of gas concentrations and proper alarm functionality.
- Calibration Accuracy: Use certified traceable test gas and verify the concentration before its expiration date to ensure accuracy.
- Environmental Conditions: Perform calibration under environmental conditions similar to the actual workplace to ensure sensor accuracy.
- Maintenance and Record-Keeping: Maintain detailed calibration records for the life of each instrument to track maintenance needs and performance.
- Training Requirements: Proper training must be provided on calibration and maintenance procedures to ensure safe and effective use of the equipment.
For comprehensive details on OSHA's regulations and guidelines for air monitoring equipment, you can visit OSHA's Direct-Reading Instruments
These steps are essential for using air monitoring equipment effectively, thereby protecting workers from potential hazards and ensuring safety and health compliance, avoiding legal and financial penalties, and enhancing business credibility.
Importance of Compliance
The importance of compliance in managing air monitoring equipment cannot be overstated, and OSHA emphasizes this through stringent guidelines:
- Safety and Health Compliance: Adhering to OSHA standards ensures the protection of employees from harmful pollutants, promoting a healthy work environment where everyone can feel safe.
- Avoiding Legal and Financial Penalties: Regular maintenance and checks of air monitoring systems are crucial to avoid violations that can lead to significant fines and legal issues, as detailed by OSHA.
- Enhancing Business Credibility: Compliance with air quality regulations not only protects health but also boosts your business's reputation by demonstrating a commitment to environmental and employee welfare.
Choosing the Right Air Monitoring Equipment: What to Consider
Selecting the right air monitoring equipment is essential for ensuring workplace safety and environmental compliance. Here are key features to consider:
- Detection Capabilities: Choose equipment that can detect specific gases or pollutants present in your environment, such as VOCs, carbon monoxide, and sulfur dioxide.
- Sensitivity and Range: Ensure the device is sensitive enough to detect concentration levels that you might encounter in your operations.
- Data Logging and Connectivity: Opt for devices with robust data logging capabilities and connectivity options like Wi-Fi or Bluetooth for real-time monitoring.
- Calibration and Maintenance: Select equipment that is easy to calibrate and maintain to reduce downtime and operational costs.
- Ease of Use: Look for user-friendly interfaces and simple operations to ensure all employees can use the equipment effectively without extensive training.
- Durability and Reliability: Ensure the equipment can withstand the environmental conditions of your workplace.
- Portability: If you need to conduct assessments in various locations, choose lightweight, portable devices.
- Alarm Systems: Integrated alarms are crucial for immediate response when pollutant levels exceed thresholds.
- Compliance with Standards: Make sure the equipment meets relevant standards set by bodies like OSHA and the EPA.
- After-Sales Support: Good after-sales support can greatly enhance the value of your air monitoring equipment.
By focusing on these features, you can select a system that not only meets regulatory requirements but also protects employee health and contributes to a safer workplace.
Different Types of Air Monitoring Equipment
Whether you want to ensure workplace safety, environmental compliance, or public health, understanding the different types of air monitoring equipment and their specific applications can help you make informed decisions.
Here’s a breakdown of the common types of air monitoring equipment and what each type is best used for:
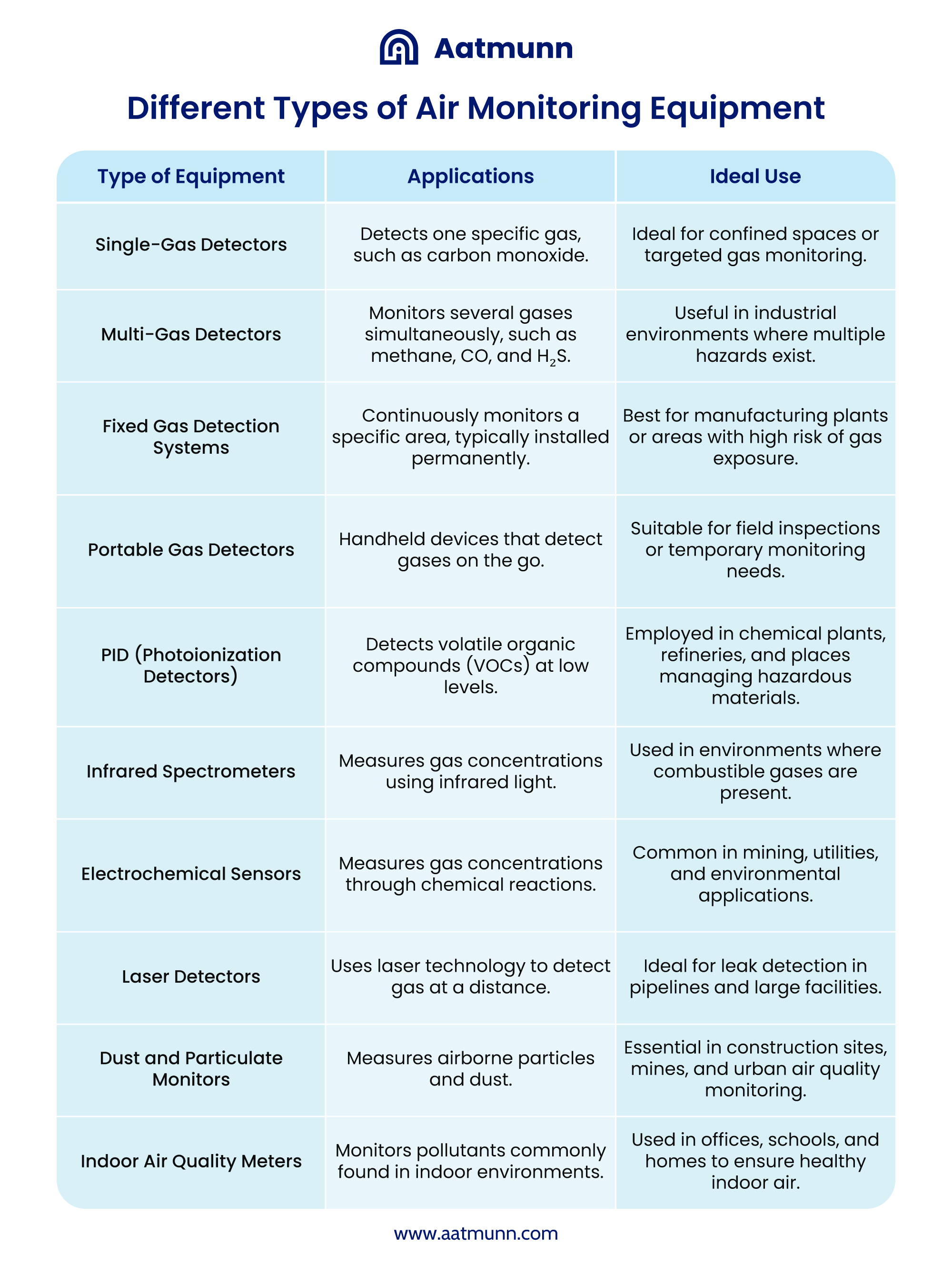
By selecting equipment suited to the specific challenges and hazards of your industry or location, you can effectively monitor air quality and ensure safety and compliance with environmental standards.
Essential Inspection Checklist for Air Monitoring Equipment
Regular inspection and maintenance of air monitoring equipment are crucial to ensure accurate readings and the safety of both the environment and personnel.
Air Monitoring Equipment Inspection Sheet
The following table serves as a comprehensive checklist to be used during the inspection of various types of air monitoring equipment:
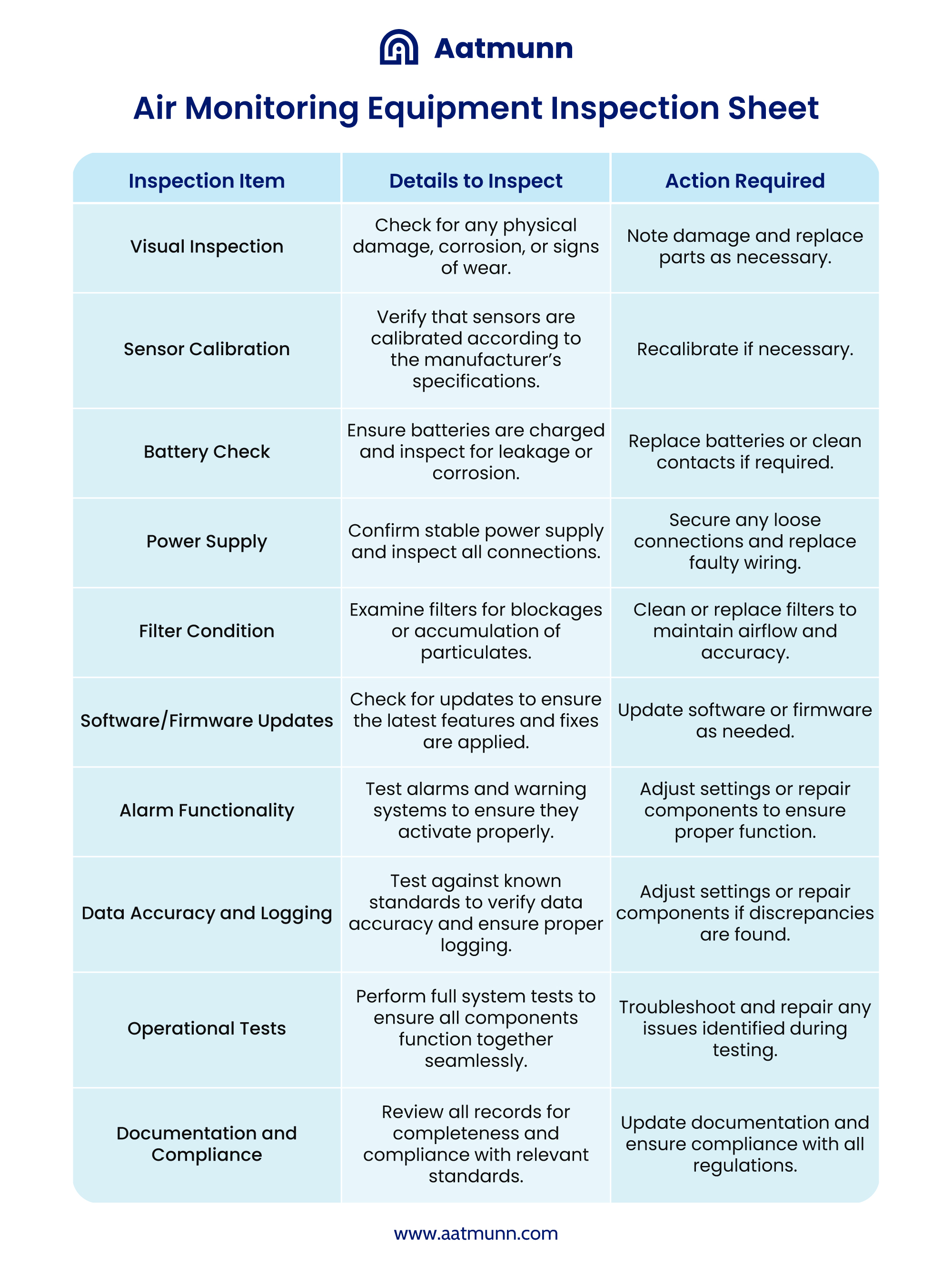
For a detailed approach to safety glasses maintenance, check out our comprehensive safety glasses inspection checklist here.
How to Use the Inspection Sheet
To effectively use an inspection sheet in alignment with OSHA standards, consider the following structured approach:
- Schedule Regular Inspections: Establish a routine—daily, weekly, or monthly—based on operational needs and OSHA requirements.
- Assign Trained Personnel: Assign inspections to personnel trained in both the equipment use and OSHA’s inspection criteria to ensure reliability and compliance.
- Document Findings: Accurately document each inspection’s findings for tracking performance and maintenance needs, aiding compliance with OSHA’s record-keeping requirements.
- Review and Act: Regularly analyze the documented results to identify trends and rectify issues promptly, aligning with OSHA’s emphasis on proactive safety management.
- Monthly and Annual Inspection Requirements: Incorporate specific checks such as visual inspections, sensor tests, battery checks, data accuracy verification, comprehensive calibration, software updates, deep cleaning, full functional tests, and a thorough review of maintenance logs.
Adhering to these practices helps ensure compliance with OSHA standards and maintains the integrity of your safety equipment. For more detailed guidelines, refer to OSHA’s recommendations on equipment inspection and maintenance.
Implementing an Air Monitoring Equipment Inspection Training Program
To implement an effective air monitoring equipment inspection training program in line with OSHA standards, here's a structured approach:
- Develop a Training Curriculum: Start with an overview of different types of air monitoring equipment, covering handheld devices, fixed systems, and wearable technologies. Emphasize the handling, operation, and maintenance required for each.
- Practical Training Sessions: Conduct detailed training on inspection techniques, including physical checks and sensor evaluations. Include calibration and testing procedures to ensure accurate readings and functionality.
- Software Updates and Configuration: Train on updating and configuring software, crucial as technology evolves.
- Hands-On Practice and Real-Time Feedback: Use simulated inspections to provide practical experience and immediate feedback to reinforce correct procedures.
- Documentation and Compliance: Focus on the importance of meticulous record-keeping for maintaining equipment history and meeting regulatory requirements.
- Understanding Regulations: Incorporate training on current industry regulations and standards that impact air monitoring, emphasizing the role of compliance.
- Evaluating Training Effectiveness: Use regular assessments and feedback mechanisms to gauge the training's effectiveness and make necessary adjustments.
For more detailed guidelines on OSHA’s training requirements, refer to the OSHA Training page. This resource can help ensure that your training program aligns with federal standards and best practices.
Training Frequency Guidelines
Here’s a detailed table that breaks down the optimal training frequencies for various aspects of air monitoring equipment inspection:
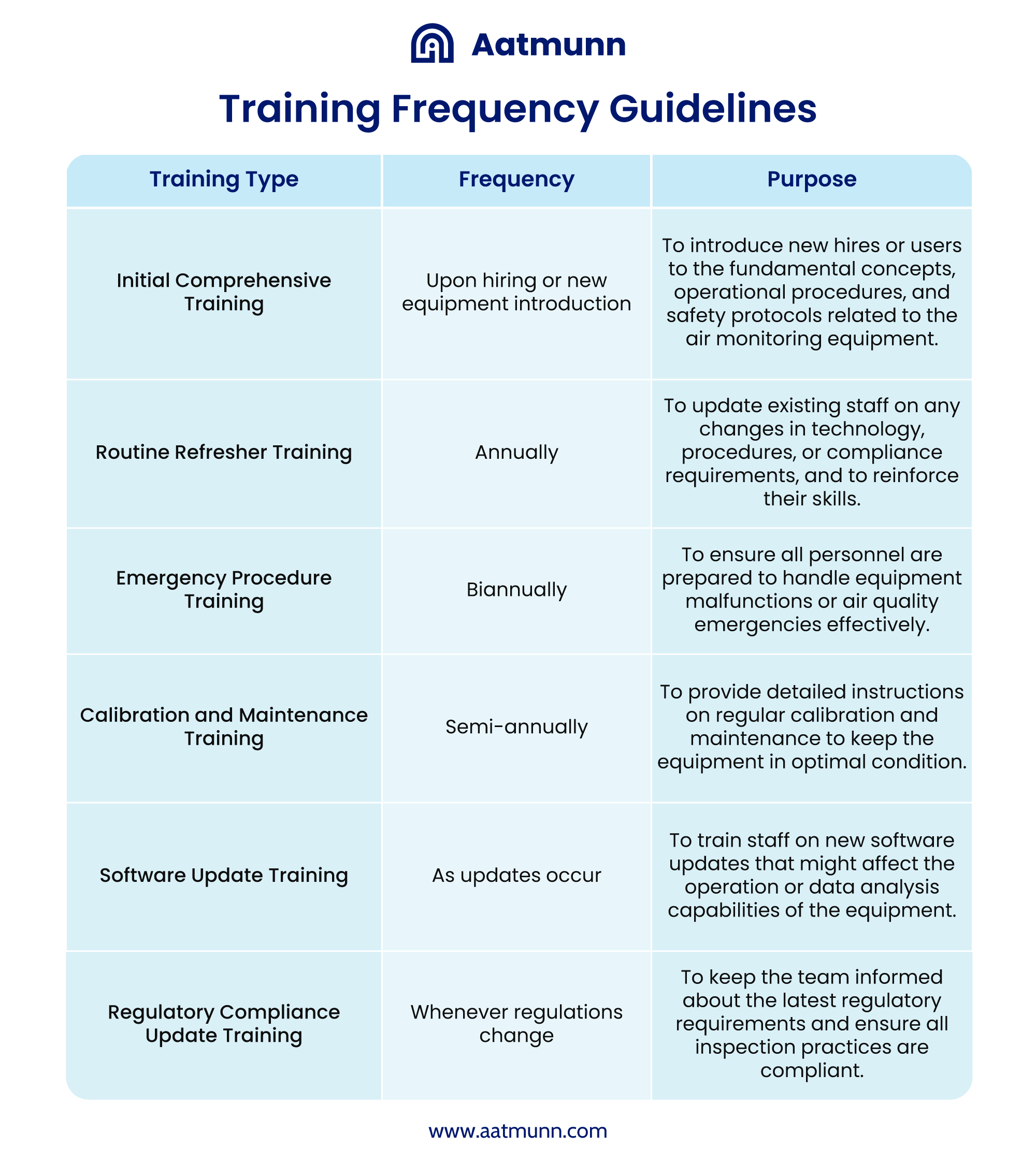
Air Monitoring Equipment Replacement Frequency Guide
Below is a table that outlines recommended replacement frequencies for various components of air monitoring equipment.
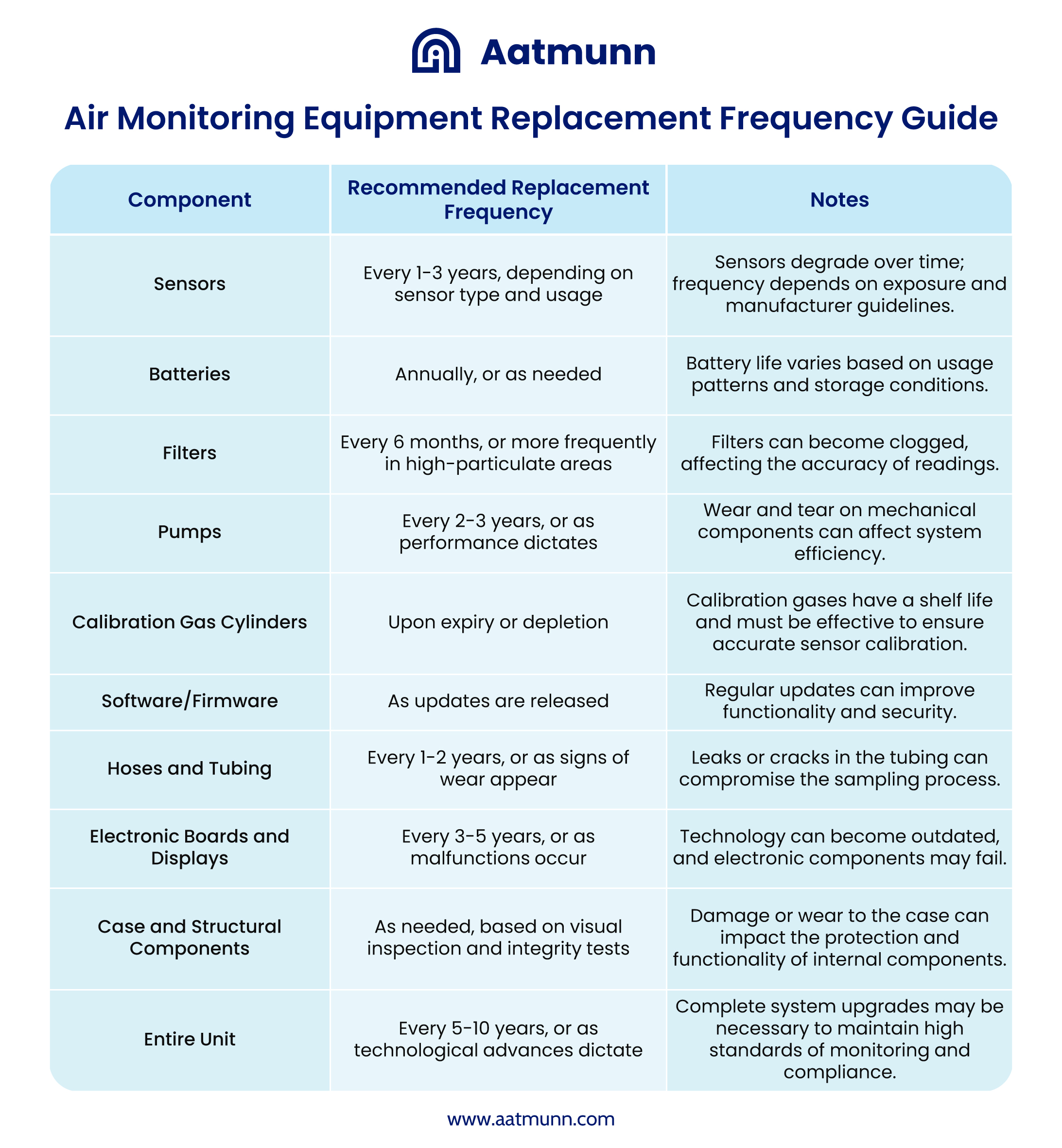
How to Use the Replacement Frequency Guide
- Assess Regularly: Regular maintenance checks can help identify when components are nearing the end of their useful life.
- Keep Records: Document each replacement and maintenance activity to track the lifecycle of each component.
- Follow Manufacturer Guidelines: Always refer to the manufacturer’s specific recommendations for replacement frequencies, as these can vary based on the model and operational conditions.
- Adapt Based on Conditions: Environmental factors such as exposure to extreme temperatures, chemicals, or high levels of particulates may necessitate more frequent replacements.
Adhering to a regular replacement schedule for air monitoring equipment ensures that all components are functioning correctly, enhancing the reliability and accuracy of air quality measurements.
Efficient Tracking Methods for Air Monitoring Equipment
Proper tracking of air monitoring equipment is crucial for ensuring timely maintenance, availability, and compliance. Here are simple and effective ways to track these vital tools.
Barcode Systems
Attach barcodes to each piece of equipment and use handheld scanners to update a central database whenever items are checked out or returned. This method is straightforward and helps keep an accurate inventory.
RFID Tags
Equip your air monitoring devices with RFID tags for real-time tracking. Scanners read the tags from a distance, making it easy to monitor equipment locations without direct contact.
GPS Tracking
For high-value or critical equipment, consider using GPS trackers. This allows for real-time location tracking, especially for equipment used across large areas or multiple sites.
Digital Management Software
Use specialized asset management software to integrate barcode, RFID, or GPS tracking data. This software can offer detailed reports on equipment usage, and maintenance schedules, and even predict when replacements might be needed.
Effective tracking of air monitoring equipment increases operational efficiency and helps maintain safety standards.
-
Identifying Common Defects in Air Monitoring Equipment
Recognizing the defects early is key to maintaining the effectiveness and reliability of your monitoring systems.
Sensor Malfunctions
Sensors are vital for detecting gases and pollutants. When malfunctioning, they may produce inaccurate readings or fail to detect hazards. Signs of sensor problems include erratic readings and failures during calibration tests.
Battery and Power Failures
Many air monitoring devices rely on batteries. Issues such as unexpected shutdowns or failure to start often indicate battery or power problems. Regular battery checks can prevent these issues.
Calibration Drift
Sensors can drift from calibration settings over time, leading to inaccurate readings. Frequent recalibration needs or calibration failures are typical signs of this problem.
Software Glitches
Software issues can affect data processing and display. Symptoms include frozen screens, unresponsive controls, or incorrect data outputs. Regular software updates and system reboots can often resolve these issues.
Physical Damage
Cracks in the casing or loose components can compromise device functionality. Physical inspections can help detect such damage early.
Clogged Filters
For devices that sample air, clogged filters can impede performance. Regular filter checks and replacements are necessary to ensure accurate air quality analysis.
To avoid these common issues, implement a routine inspection and maintenance schedule for your air monitoring equipment.
Best Practices for Cleaning and Maintaining Air Monitoring Equipment
Here are steps to ensure your devices function effectively.
Cleaning Steps
- Daily Wipe-Down: Begin each day by wiping the exterior of your air monitoring equipment with a soft, dry cloth. This removes any dust or debris that could accumulate and interfere with sensor accuracy.
- Weekly In-depth Cleaning: Use a slightly damp cloth to clean the exterior surfaces more thoroughly. Avoid using harsh chemicals or abrasive materials that could damage the equipment.
- Sensor Care: Follow the manufacturer's guidelines for cleaning sensors. Typically, this involves gently removing dust with a soft brush or using a specific cleaning solution provided or approved by the manufacturer.
Maintenance Tips
- Regular Filter Replacement: Check the filters monthly and replace them as needed to ensure airflow is not restricted. Clogged filters can lead to inaccurate readings.
- Battery Checks: For battery-operated units, check the battery level regularly and replace the batteries before they completely drain to avoid interruptions in monitoring.
- Calibration: Calibrate the equipment according to the manufacturer’s schedule. Calibration is crucial for accuracy and may need to be performed more frequently if the equipment is used in a high-pollutant environment.
- Software Updates: Keep the equipment’s software up to date. Install updates as soon as they become available to improve functionality and performance.
- Storage: When not in use, store the equipment in a clean, dry place. Proper storage prevents exposure to harmful conditions that could degrade components.
For specific guidelines on equipment maintenance, please refer to OSHA’s Equipment Maintenance document.
Top US Brands for Air Monitoring Equipment
Here’s a look at some of the top US brands that specialize in high-quality air monitoring systems, known for their reliability and innovative technology.
Leading US Brands in Air Monitoring Equipment
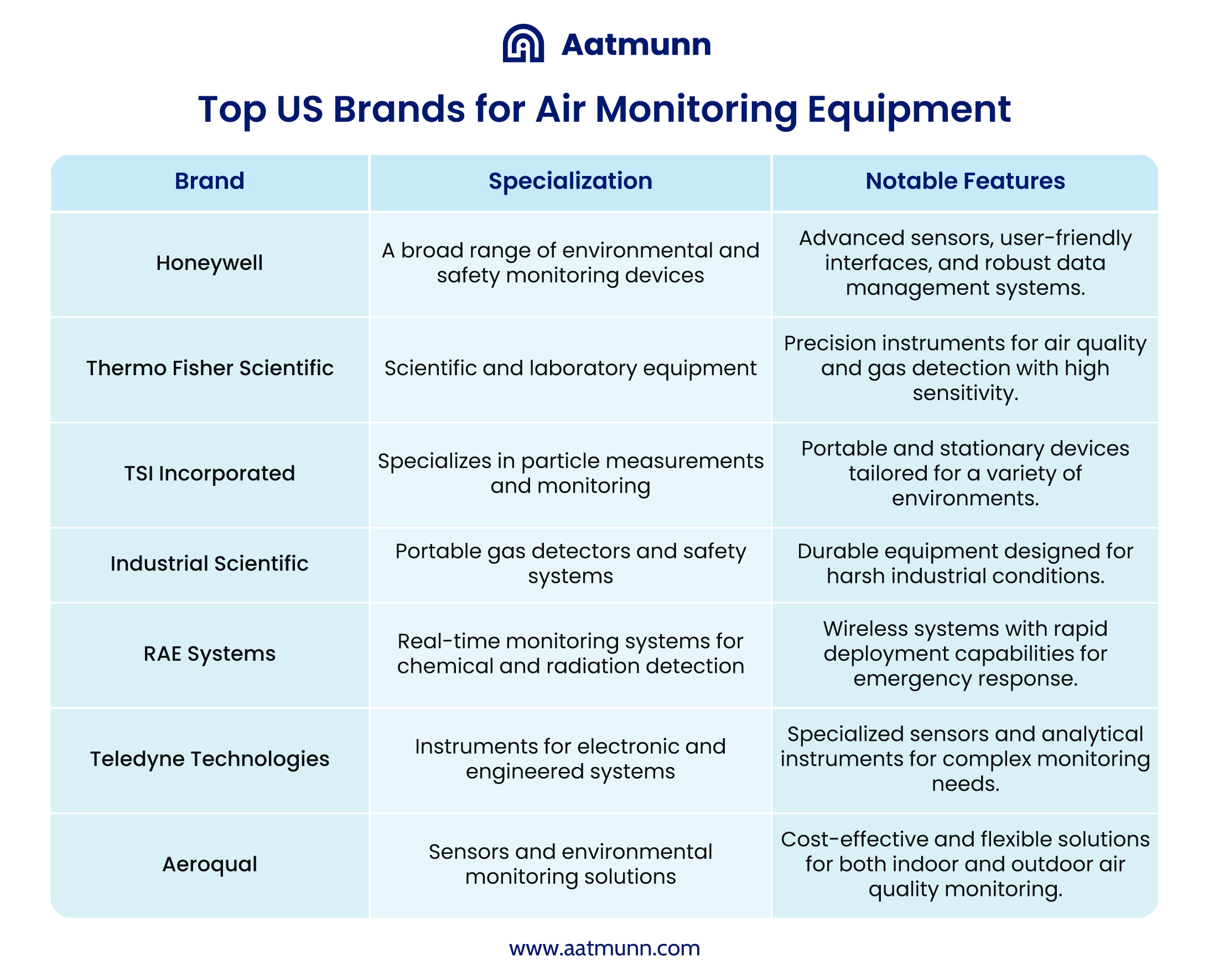
Choosing a brand from this list ensures you are investing in quality equipment that will provide accurate readings and withstand the demands of any operational environment.
Industry-Specific Guide to Air Monitoring Equipment
Selecting the right air monitoring equipment tailored to specific industry needs is crucial for maintaining safety and compliance with regulatory standards.
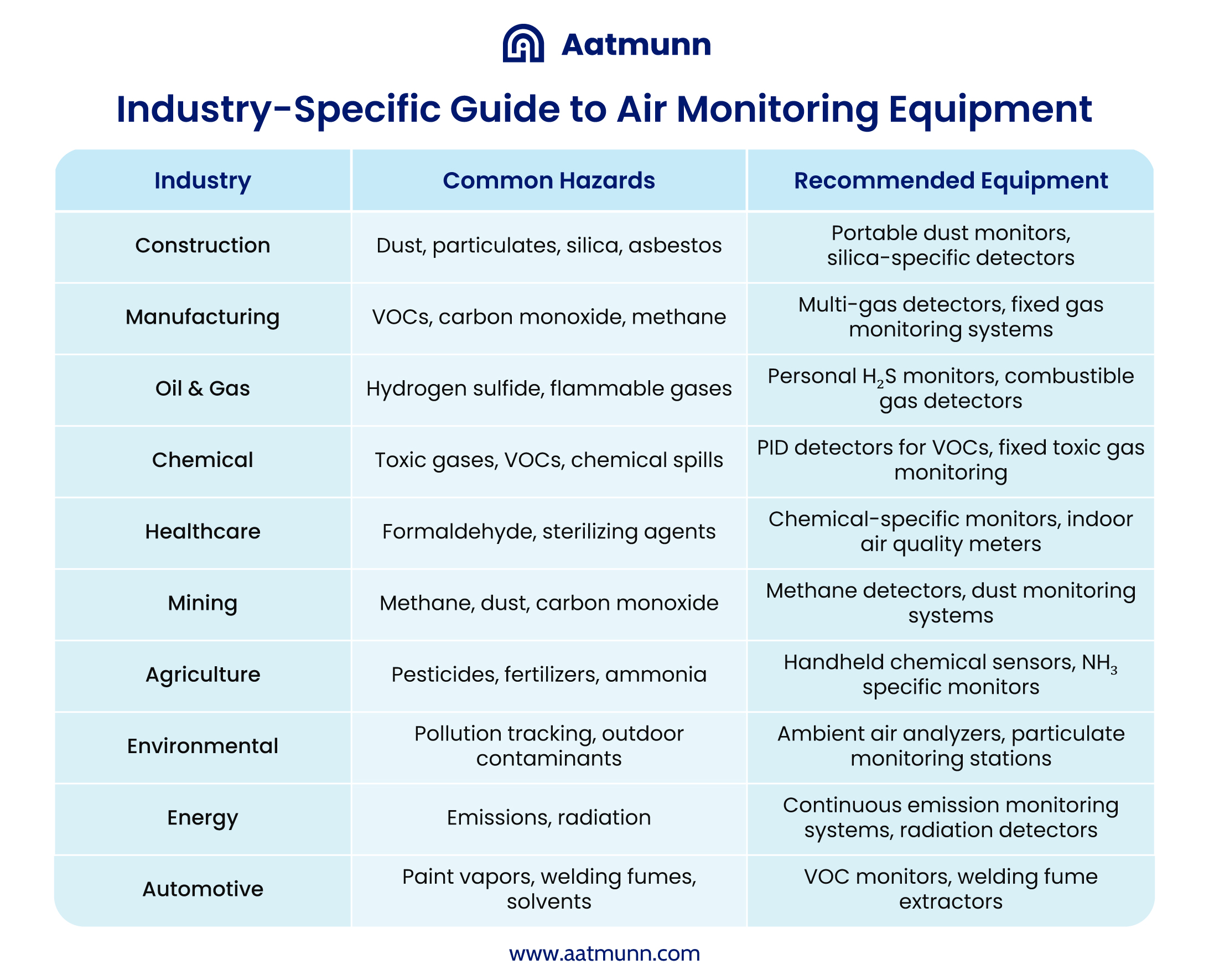
By investing in the right equipment, industries can protect their workers, avoid compliance issues, and maintain efficient and safe operations.
Enhancing Air Monitoring Equipment Inspections with Safety Inspection Manager (SIM)
Air monitoring is crucial for protecting health in various environments, highlighted by reports from organizations like WHO and UNEP which link poor air quality to significant health issues. Safety Inspection Manager (SIM) significantly advances compliance and safety practices for air monitoring equipment inspections.
Key Features of SIM for Air Monitoring Equipment:
- Automated Compliance Management: SIM updates its system with the latest OSHA standards and guidelines, ensuring that air monitoring equipment meets all regulatory requirements.
- Real-Time Monitoring and Alerts: The system provides instant notifications for any deviations or malfunctions in equipment, enabling immediate corrective action.
- Comprehensive Record-Keeping: SIM maintains detailed logs of inspections, calibrations, and maintenance actions, essential for audits and regulatory reviews.
- Efficient Calibration and Maintenance Schedules: The software ensures that all air monitoring equipment is regularly tested and calibrated, adhering to OSHA’s requirements for accuracy and reliability.
- Training and Compliance Enhancement: SIM includes training modules to educate workers on the latest air monitoring practices and compliance standards, ensuring knowledgeable handling of equipment.
- Customizable Inspection Checklists: Users can modify checklists to address specific monitoring needs and regulatory changes, enhancing the thoroughness of inspections.
Benefits of Using SIM:
- Streamlined Inspection Processes: Automates scheduling and standardizes inspections, reducing errors and oversight.
- Enhanced Safety and Compliance: Keeps equipment compliant with health and safety regulations, safeguarding worker health and avoiding legal or financial penalties.
- Improved Operational Efficiency: Reduces downtime by maintaining equipment in peak condition through regular inspections and maintenance.
OSHA Compliance
SIM aligns with OSHA's requirements for air monitoring equipment, such as daily calibration tests and accurate record-keeping, making it an indispensable tool for organizations aiming to meet stringent safety standards.
By integrating Safety Inspection Manager into your safety protocols, you can significantly enhance the effectiveness and reliability of your air monitoring equipment inspections, ensuring a safer work environment