Eye safety in the workplace is critical, with an estimated 2,000 workers suffering eye injuries each day. These injuries not only result in significant personal trauma but also incur substantial financial costs for employers and insurance companies. According to the U.S. Bureau of Labor Statistics (BLS), these injuries result in over $924 million annually in workers’ compensation and nearly $4 billion in wage and productivity losses. Conducting regular inspections of safety glasses is an essential practice to mitigate these risks and ensure employee protection.
Navigating OSHA Requirements for Safety Glasses
OSHA has specific safety glasses requirements under its personal protective equipment (PPE) standards. These requirements aim to ensure employees' safety from eye and face hazards in the workplace. Here are the key points from the OSHA guidelines:
OSHA Standards for Safety Glasses
General Industry (29 CFR 1910.133)
- Employers must provide appropriate eye and face protection to employees who are exposed to hazards such as flying particles, molten metal, liquid chemicals, acids, chemical gases or vapors, or potentially injurious light radiation.
- Safety glasses must comply with the ANSI Z87.1-1989 standard for occupational and educational eye and face protection.
Construction Industry (29 CFR 1926.102)
- Like the general industry, employers must ensure that employees use appropriate eye and face protection when exposed to eye or face hazards.
- The provided safety glasses should meet the requirements of the ANSI Z87.1-1968 standard, or later versions.
Maritime (29 CFR 1915.153)
- Eye and face protection must be provided to employees when there is a reasonable probability of injury that can be prevented by such equipment.
- The protection must conform to the ANSI Z87.1-1989 standard.
For more detailed information and specific regulatory requirements, you can refer to the following links:
General Industry Eye and Face Protection (29 CFR 1910.133)
Construction Eye and Face Protection (29 CFR 1926.102)
Maritime Eye and Face Protection (29 CFR 1915.153)
These resources provide comprehensive guidelines and ensure that employers are compliant with OSHA standards to protect their workers effectively.
Legal Implications of Non-Compliance
- Fines and Penalties: Failure to comply with OSHA, ANSI, or local safety standards can result in fines and penalties. These can be substantial, depending on the severity of the non-compliance and the specific regulations violated.
- Increased Liability: Employers who fail to provide adequate eye protection may face increased liability in the event of an injury. This can lead to costly lawsuits and damage to the company’s reputation.
- Worker Compensation Claims: Non-compliance can lead to higher incidents of workplace injuries, resulting in more worker compensation claims and higher insurance premiums.
By understanding and adhering to the legal and regulatory requirements for safety glasses, employers can protect their employees from eye injuries and minimize the risk of legal and financial penalties.
Different Types of Safety Glasses and Their Uses
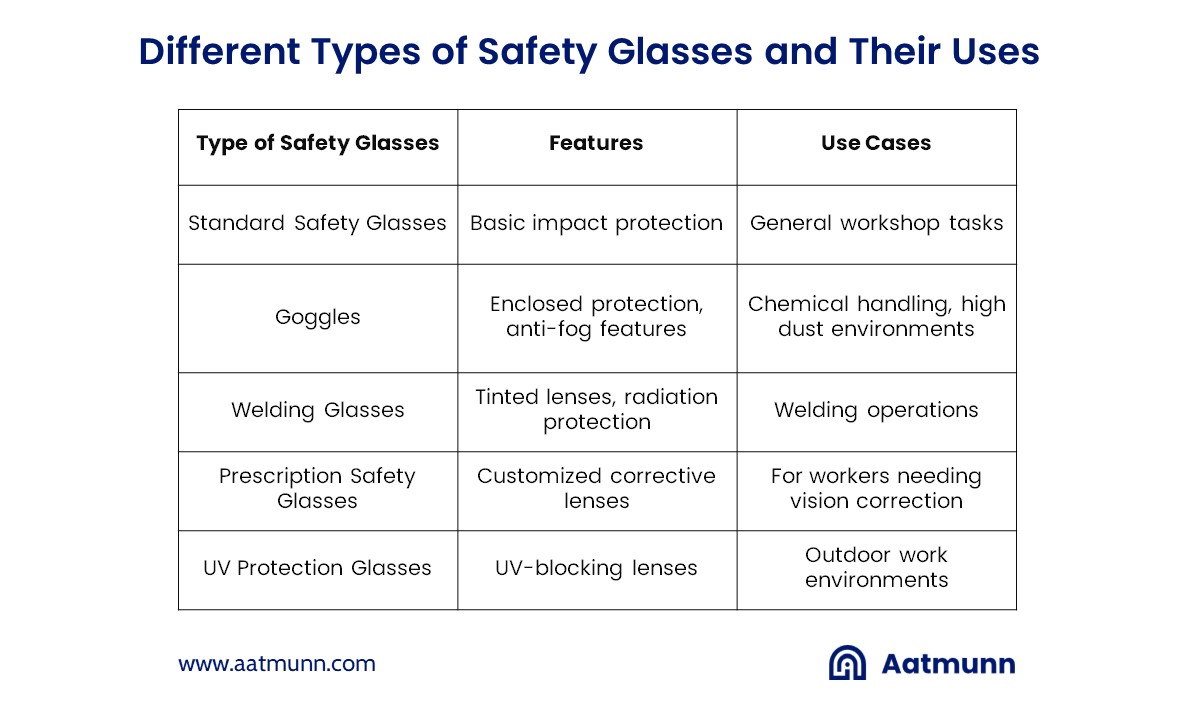
Understanding the specific applications and risks associated with each type of safety glasses is essential to ensure appropriate eye protection in various work scenarios.
Choosing the Right Safety Glasses for Maximum Protection
Before selecting safety glasses, it's essential to assess the specific risks associated with your workplace. Different environments pose unique hazards, and the safety glasses you choose must be suitable to protect against those specific dangers. Common risks include:
- Physical impacts: From large debris at construction sites to fine particulates in woodworking shops.
- Chemical splashes: Especially prevalent in laboratories and manufacturing plants.
- Radiation exposure: Such as UV light from welding or excessive sunlight.
Safety Standards and Certifications
Ensure the safety glasses you select meet the required safety standards. In the United States, the American National Standards Institute (ANSI) Z87.1 is a common standard that provides guidelines for eye protection. Glasses that meet this standard will have "Z87" or "Z87+" marked on the frame or lens, indicating they are certified to provide adequate protection:
- Z87: Basic impact protection suitable for general use.
- Z87+: High-impact protection for more hazardous environments.
Key Features to Consider
When choosing safety glasses, consider the following features to ensure maximum protection and comfort:
- Lens Material: Polycarbonate lenses are popular for their high impact resistance and lightweight properties. For environments with no impact hazards but potential exposure to chemicals, acetate lenses might be preferable due to better chemical resistance.
- Lens Coating: Anti-fog and anti-scratch coatings can enhance visibility and durability. UV protective coatings are essential for outdoor work to protect against harmful ultraviolet radiation.
- Frame Design: The right frame design can enhance protection and comfort. Options include:
- Wraparound frames offer better peripheral protection.
- Goggles provide a secure fit and protection from all angles, suitable for high-risk areas involving chemical exposure or fine particulates.
- Over-the-glass (OTG) designs accommodate workers who wear prescription glasses.
- Fit and Comfort: Ensure the safety glasses fit well without slipping. Adjustable frames, nose pieces, and padded temples can increase comfort, encouraging consistent use.
- Special Considerations
- Prescription Safety Glasses: For employees who wear prescription glasses, prescription safety glasses are a must. These should also meet the ANSI Z87.1 standards to ensure they provide both correct vision and protection.
- Tinted Lenses: For outdoor work, consider tinted lenses to reduce glare and eyestrain from bright sunlight.
Selecting the right safety glasses involves more than just picking a pair off the shelf. It requires an understanding of workplace hazards, adherence to safety standards, and consideration of features that enhance protection and comfort.
Myths Debunked: Do Safety Glasses Damage Your Eyesight?
Safety glasses are designed to protect your eyes and do not harm your eyesight when used correctly. They shield your eyes from hazards like debris and chemicals. However, discomfort or strain can occur if the glasses are improperly fitted or incorrectly prescribed. It's crucial to ensure that safety glasses are well-fitted and, for those requiring corrective lenses, that they are accurately prescribed to avoid any vision issues while still providing essential protection.
Importance of Regular Testing for Safety Glasses
Safety glasses testing ensures that safety glasses meet specific safety standards and continue to offer reliable protection, helping to prevent eye injuries and maintain compliance with occupational safety regulations.
Standards for Testing Safety Glasses
Safety glasses are tested according to specific standards that define the criteria for impact resistance, durability, and lens clarity. The most commonly recognized standards include:
- ANSI Z87.1: In the United States, the American National Standards Institute (ANSI) Z87.1 standard specifies performance requirements and testing methods for eye protection. Safety glasses must pass rigorous tests for high mass and high-velocity impacts, penetration, and exposure to non-ionizing radiation and chemicals to be ANSI Z87.1 certified.
- EN 166: In Europe, safety glasses must comply with EN 166, a standard similar to ANSI Z87.1 but with some variations in classification and testing requirements. It ensures that safety glasses provide adequate protection against common hazards like flying particles and molten metal.
Testing Procedures for Safety Glasses
The testing of safety glasses involves several key procedures that simulate real-world conditions:
- Impact Tests: Safety glasses undergo high-velocity and high-mass impact tests to simulate the effect of flying objects hitting the lenses at different speeds and weights. These tests ensure the lenses can resist shattering or significant deformation.
- Durability Tests: Durability tests include assessing the frame's strength and the lens's resistance to ageing, exposure to sunlight, extreme temperatures, and corrosion.
- Optical Clarity Tests: To ensure that safety glasses do not impair vision, optical clarity tests are performed. These tests evaluate the refractive properties and light diffusion of the lenses.
- Coverage Tests: Safety glasses are also tested for their coverage area, ensuring that they provide adequate protection not just directly in front of the eyes but also peripherally.
These are not the only types of testing that the standards of your destination market may require. It’s important to tailor your testing protocols to your unique needs and market location.
Why Regular Testing is Essential
Regular testing of safety glasses is critical for several reasons:
- Safety Assurance: Consistent testing helps manufacturers and employers ensure that safety glasses continue to provide the required level of protection.
- Regulatory Compliance: Meeting testing standards like ANSI Z87.1 and EN 166 is necessary for legal compliance and avoiding potential fines and liabilities.
- Innovation and Improvement: Ongoing testing drives innovation, leading to the development of more effective and comfortable safety glasses.
Regular testing not only helps in complying with legal standards but also plays a crucial role in fostering a culture of safety and prevention in the workplace.
Avoiding Common Safety Glasses Mistakes: Essential Tips
1. Incorrect Fit
- Many workers experience injuries simply because their safety glasses don't fit properly, which can cause the glasses to slip off or fail to fully protect the eyes.
- Ensure that safety glasses are adjustable and properly fitted to each individual's face. Conduct fit tests during the initial distribution of the glasses.
2. Using Damaged Glasses
- Continuing to wear safety glasses that have scratches, cracks, or other damages not only obstructs vision but also compromises the structural integrity of the glasses.
- Regularly inspect safety glasses for any signs of wear or damage and replace them immediately if defects are found.
3. Inappropriate Style for the Hazard
- Using safety glasses that are not designed for the specific type of hazard encountered can lead to serious eye injuries.
- Identify the specific hazards in your workplace and choose safety glasses that are designed to protect against those particular risks.
4. Lack of Compliance with Safety Standards
- Skipping the step of ensuring that safety glasses meet relevant safety standards is a common oversight that can have dire consequences.
- Only purchase and use safety glasses that are certified to meet or exceed national safety standards, such as ANSI Z87.1 in the United States.
5. Poor Maintenance and Cleaning
- Failing to properly maintain and clean safety glasses can lead to reduced visibility and increased risk of contamination.
- Provide proper storage cases and cleaning materials, and train employees on how to care for their glasses correctly.
Avoiding these common mistakes with safety glasses is crucial for ensuring they provide the maximum level of protection.
Streamlining Your Safety Glasses Inspection Routine
To maintain the integrity and effectiveness of safety glasses, it's essential to conduct regular inspections. Below is a comprehensive checklist that can be used daily, monthly, and before any critical task where eye protection is required.
Safety Glasses Checklist
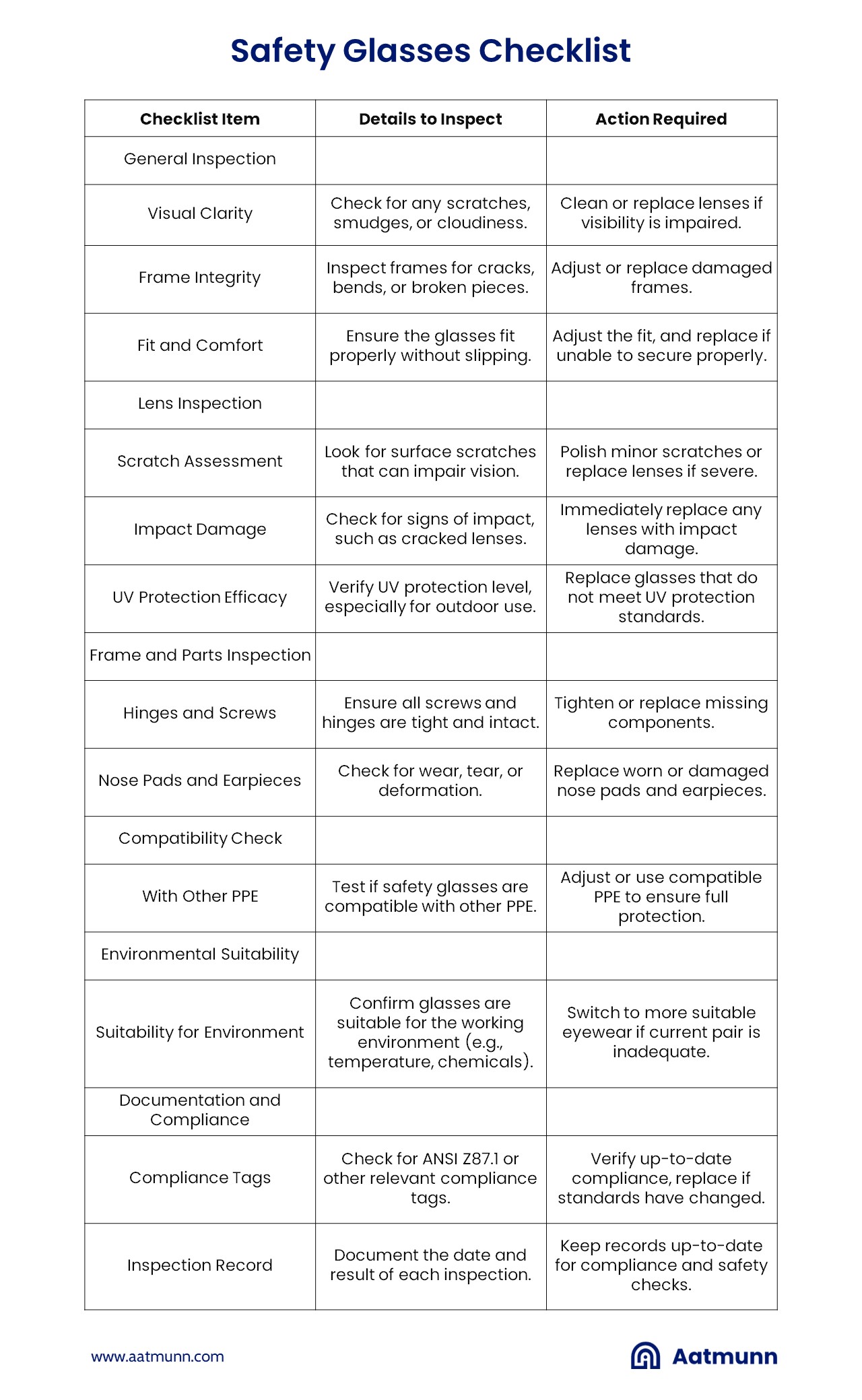
For a detailed approach to safety glasses maintenance, check out our comprehensive safety glasses inspection checklist here.
Recommended Safety Glasses Inspection Frequency
To ensure safety glasses remain in optimal condition and provide the necessary level of protection, organizations should adhere to the following inspection frequency:
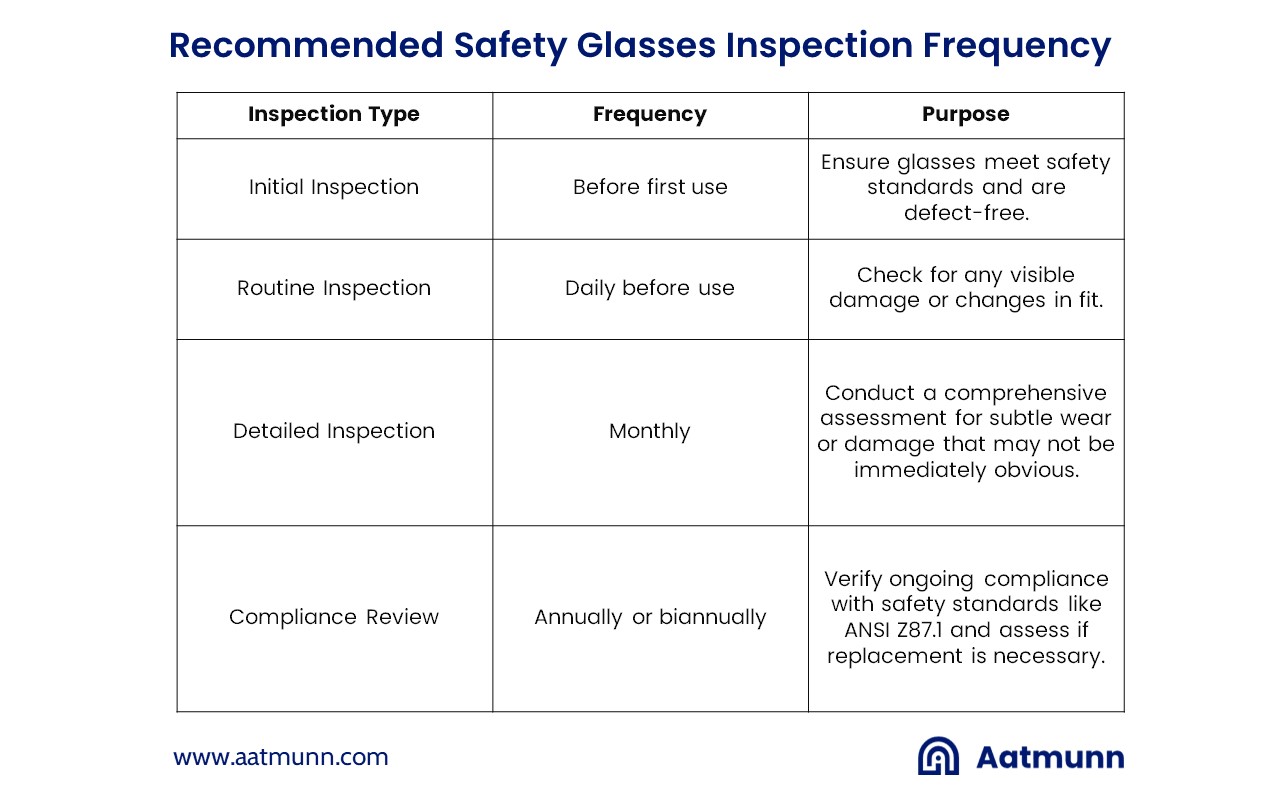
Monthly Safety Glasses Inspection Requirements
Monthly inspections are designed to catch issues before they compromise the safety and effectiveness of the glasses. This frequent check helps to maintain the integrity of the safety equipment in environments with regular exposure to hazards.
Monthly Inspection Checklist:
- Visual Clarity: Ensure lenses are free of scratches, cracks, or other damage that may impair vision.
- Lens Integrity: Check for any signs of wear, such as cracks or deep scratches that could affect the lenses' structural integrity.
- Frame Condition: Examine frames for any signs of damage or deformation. Ensure that all parts, including the arms and nose pads, are intact and securely attached.
- Fit and Comfort: Confirm that the glasses still fit securely on the face without slipping. Check the condition of adjustable parts for proper function.
- Cleanliness: Glasses should be clean, and free from dust, dirt, and smudges to ensure clear visibility.
- Side Shields: If applicable, ensure side shields are securely attached and undamaged.
- Functionality of Features: For glasses with special features like anti-fog or UV protection, check that these features are still functioning effectively.
- Documentation: Record the findings from each monthly inspection to track the condition over time and replace or repair glasses as needed.
Annual Safety Glasses Inspection Requirements
The annual inspection is more comprehensive, and intended to assess the overall lifespan and continued usability of the safety glasses. This inspection ensures that each pair of safety glasses still meets safety standards and provides adequate protection.
Annual Inspection Checklist:
- Comprehensive Lens Check: Perform a detailed examination of the lenses for any subtle damages or changes in optical clarity that might have been overlooked during monthly inspections.
- Full Frame Assessment: Check the entire frame for stress fractures, corrosion (particularly in metal frames), and other potential failures.
- Complete Fit Evaluation: Reassess the fit to ensure that changes in the frames have not affected how the glasses rest on the face, especially after prolonged use.
- Special Features Inspection: Thoroughly test all additional protective features like UV and anti-fog effectiveness, which may degrade over time.
- Replacement Parts: Check the availability and condition of any replaceable parts like nose pads or side shields.
- Safety Standard Compliance: Verify that the safety glasses still comply with current safety standards (e.g., ANSI Z87.1 or EN 166) as regulations may have been updated.
- Documentation: Update the inspection records with detailed findings from the annual check. Schedule replacements or maintenance as necessary based on the inspection results.
Tips for Conducting Effective Inspections
- Train Employees: Ensure all employees are trained on how to perform daily and detailed inspections.
- Create Inspection Checklists: Develop comprehensive checklists based on the types of safety glasses used and specific workplace hazards.
- Document Inspections: Keep records of all inspections, including the inspector's name, date, and any actions taken following the inspection.
- Regular Updates: Regularly review and update inspection procedures to accommodate new safety standards or changes in workplace conditions.
By establishing and following a structured inspection regime, organizations can significantly reduce the risk of eye injuries and ensure compliance with occupational safety standards.
Training Program for Safety Glasses Inspection
Training workers on how to correctly inspect safety glasses is not just about compliance with safety regulations—it's about protecting employees from preventable injuries. Proper training ensures that every pair of safety glasses is up to standard before being used in hazardous environments.
Components of an Effective Training Program
- Understanding of Safety Standards: Employees must be familiar with relevant safety standards like ANSI Z87.1, which covers the requirements for various types of eye protection. Knowledge of these standards is crucial for understanding why inspections are necessary.
- Identification of Defects: Workers need to recognize signs of wear and damage, such as scratches, cracks, or warped frames that could impair the protective quality of the glasses.
- Hands-On Inspection Techniques: Effective training should teach employees how to conduct thorough inspections, including checking the fit, ensuring the lenses are secure, and that the frames are intact and not distorted.
- Proper Documentation Practices: Workers need to learn how to document the condition of the safety glasses and report if replacements are needed.
- Interactive Learning Sessions: Include interactive components such as quizzes or practical demonstrations to engage participants and reinforce learning.
Safety Glasses Inspection Training Frequency
Consistent training is key to ensuring that employees retain the necessary skills to inspect safety glasses effectively. Here's a suggested schedule for training frequency:
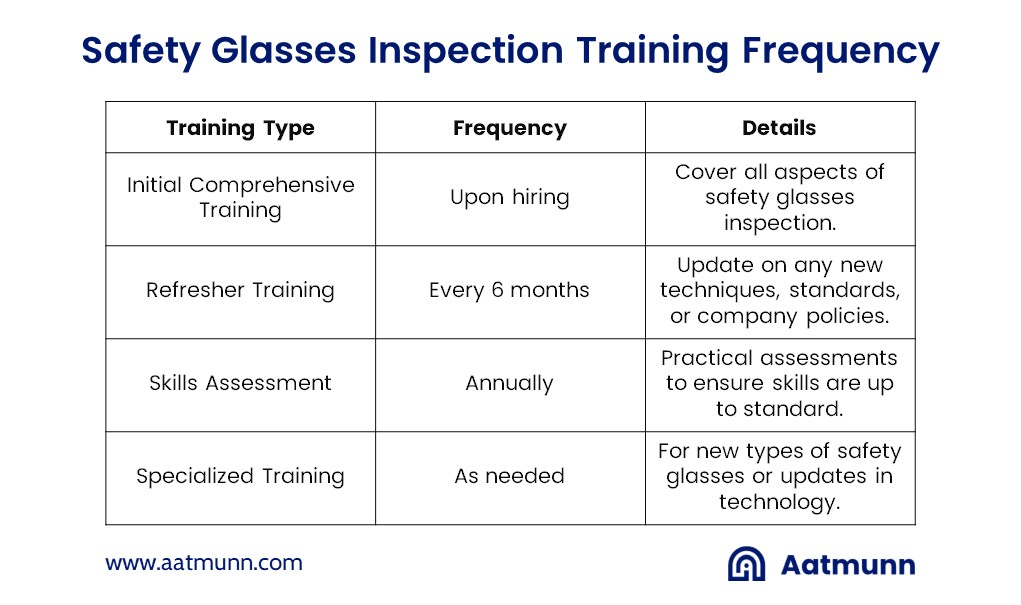
Steps to Implement the Safety Glasses Training Program
- Develop a Curriculum: Create a detailed curriculum that covers all necessary topics, from the basics of eye safety to the specifics of inspection protocols.
- Select Qualified Instructors: Choose instructors who have expertise in workplace safety and are skilled in teaching adult learners.
- Schedule Training Sessions: Plan sessions according to the frequency table, ensuring all new hires receive immediate training and existing employees are kept up-to-date.
- Utilize Diverse Teaching Methods: Incorporate a mix of lectures, discussions, video demonstrations, and hands-on practice to cater to different learning styles.
- Evaluate and Adapt: Regularly assess the effectiveness of the training program through feedback and performance during skills assessments. Adapt the training as necessary to address any gaps or changes in safety standards.
A robust training program for safety glasses inspection is essential for maintaining workplace safety and ensuring compliance with safety regulations.
Comprehensive Safety Glasses Inspection Sheet
Below is an example of how an effective safety glasses inspection sheet might be structured. This table format ensures all relevant aspects are checked and recorded systematically:
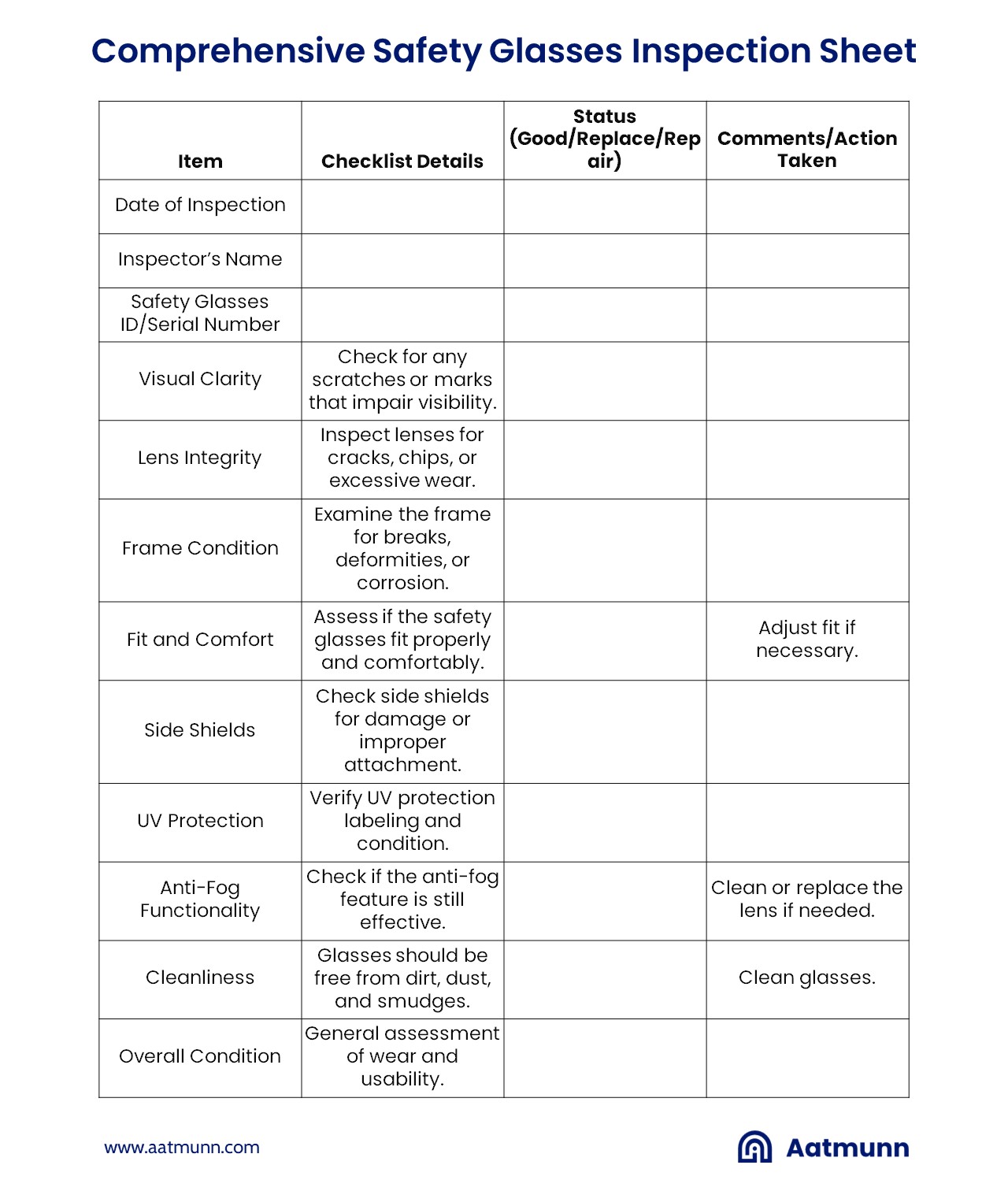
How to Use the Inspection Sheet
- Before Use: Inspect safety glasses before each use, especially in environments with high risk of eye hazards.
- Monthly Checks: Conduct a detailed inspection using the sheet at least once a month to ensure ongoing compliance and safety.
- After Incident: Perform an inspection if the safety glasses have been involved in an incident or exposed to significant impact or chemical exposure.
Regular use of this inspection sheet can help prevent workplace injuries and ensure compliance with safety regulations, ultimately fostering a safer working environment.
When to Replace Safety Glasses: Key Factors to Consider
To maintain the highest level of eye protection in hazardous work environments, it's crucial to adhere to a structured replacement timeline for safety glasses.
- Lens Condition: Scratches, cloudiness, or damage from impacts can impair vision and reduce protection. These conditions can compromise safety and require replacement.
- Frame Wear: Over time, frames may become bent, broken, or otherwise unfit, affecting how the glasses fit and protect the wearer.
- Updated Standards: Safety standards evolve, and older models may not comply with new regulations, necessitating updates to newer, compliant models.
- Technological Advances: Innovations in safety glasses, such as improved UV protection, anti-fog technologies, and better material durability, might prompt replacements to take advantage of these features.
Safety Glasses Replacement Timeline
After Any Damage or Impact Incident
- Immediately: Replace safety glasses immediately if they suffer any significant impact or visible damage, as their ability to protect is likely compromised.
Annual Checks for Standard Use
- Every 12 Months: Conduct a thorough inspection annually and replace any glasses that show signs of significant wear, such as deep scratches or cracks, frame damage, or compromised side shields.
High-Intensity Work Environments
- Every 6 Months: In settings with high exposure to debris, chemicals, or intense light, more frequent replacements might be necessary due to quicker degradation of protective features.
UV Exposure
- Every 12-24 Months: For safety glasses used predominantly outdoors, check UV protection effectiveness annually and consider replacement every two years, as the UV blocking effectiveness can degrade with prolonged exposure to sunlight.
When Manufacturer Recommendations Dictate
- As Recommended: Always adhere to the manufacturer’s specific guidelines for replacement timelines, as different materials and designs may have unique durability.
Adhering to a structured safety glasses replacement timeline is crucial for maintaining the safety and well-being of employees in hazardous work environments.
Who Needs Safety Glasses? Insights Across Industries
Safety glasses are recommended for people who work in or around potentially dangerous conditions. Here’s a table outlining the key eye protection needs and suitable safety glasses for different industries:

By understanding the unique hazards of each industry and selecting appropriate safety glasses, employers can ensure enhanced protection, compliance, and comfort.
Streamlining Safety Glasses Tracking in the Workplace
Maintaining an accurate inventory and usage tracking system for safety glasses is crucial. Effective tracking not only ensures compliance with safety regulations but also optimizes the management of personal protective equipment (PPE). Here’s how organizations should implement a robust safety glasses tracking system.
- Barcoding and Scanning: Assign barcodes to each pair of safety glasses. Employees can scan these barcodes when taking or returning safety glasses, which automatically updates the inventory system.
- RFID Tags: For larger facilities, RFID tags can be more efficient. These tags allow for real-time tracking of safety glasses without the need for manual scanning, as they can be detected and logged by proximity readers.
- Digital Management Software: Use digital asset management software tailored for PPE. These platforms can store detailed records, automate alerts for maintenance, and generate usage reports to aid in decision-making.
- Regular Audits: Despite automated systems, regular manual checks and audits are crucial to verify the accuracy of the tracking system and the actual physical condition of the safety glasses.
A well-implemented safety glasses tracking system is a valuable asset for any safety-conscious organization.
Best Practices for Cleaning and Maintaining Safety Glasses
Here are essential tips on how to clean and maintain safety glasses, ensuring they continue to offer the best possible protection.
Cleaning Safety Glasses
- Use Proper Materials: Always use a soft, lint-free cloth to clean the lenses. Avoid using materials that could scratch or damage the lens surface, such as paper towels or rough fabrics.
- Choose Appropriate Cleaners: Utilize cleaning solutions specifically designed for eyewear to prevent damage to the lenses or coatings. Avoid household cleaners like Windex, which can degrade lens coatings.
- Gentle Washing: For a thorough clean, rinse the glasses under lukewarm water to remove any dust and debris. Apply a small amount of lens cleaning solution to each lens, gently rub across the lens in a circular motion with a microfiber cloth, and then rinse again.
- Air Dry or Pat Dry: After washing, either let the glasses air dry or gently pat them dry with a clean, dry microfiber cloth. This method prevents water spots and does not scratch the lenses.
Maintaining Safety Glasses
- Regular Inspections: Check your safety glasses regularly for scratches, cracks, or other damages. Inspect the fit to ensure they haven't become loose or uncomfortable, which could affect protection.
- Proper Storage: When not in use, store your safety glasses in a clean, dry place. Using a protective case can prevent scratches and other damage when the glasses are not being worn.
- Replacement Schedule: Even with proper care, safety glasses should be replaced periodically to maintain optimal protection, especially if the lenses become scratched or the frames are bent or broken.
- Handling With Care: Always handle your safety glasses with care. Avoid leaving them in places where they might be subjected to physical damage or extreme temperatures, which can warp or alter the structure.
By following these straightforward cleaning and maintenance tips, you can safeguard your vision effectively in any work environment.
Top Safety Glasses Brands in the U.S.
Here's a table showcasing some of the premier brands for safety glasses in the USA, highlighting what each brand is renowned for:
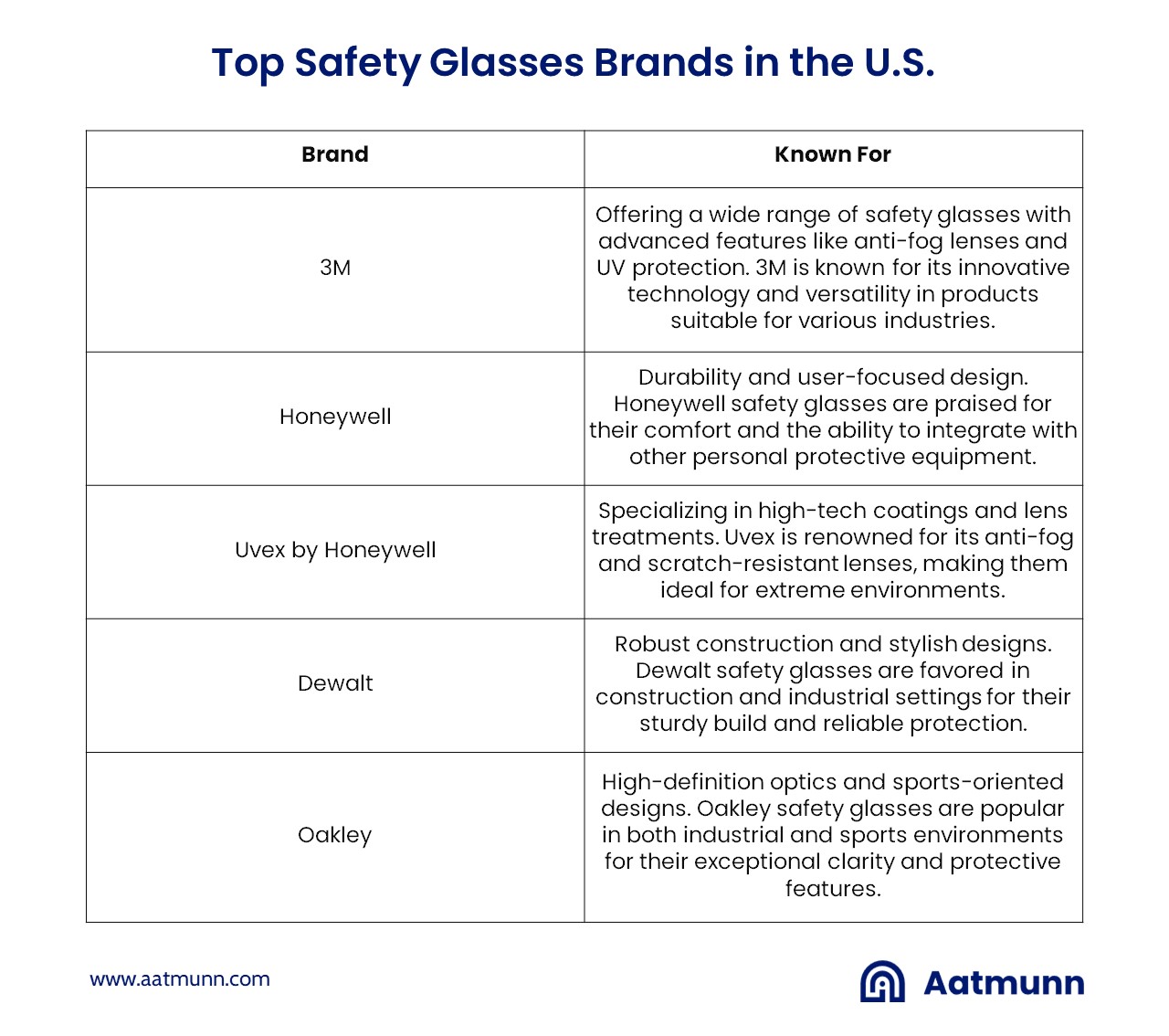
Selecting the right brand of safety glasses is critical not only for ensuring compliance with safety regulations but also for providing optimal protection and comfort to users.
Enhancing Safety Glasses Inspection with Safety Inspection Manager (SIM)
Safety glasses are essential in protecting workers from potential hazards. Implementing a Safety Inspection Manager (SIM) can transform the efficiency and accuracy of safety glasses inspections, ensuring they remain in optimal condition and comply with safety regulations.
Key Functions of Safety Inspection Manager
- Automated Scheduling and Reminders: SIM automates inspection scheduling and sends reminders, minimizing human error and administrative tasks.
- Standardized Protocols: Standardize inspection criteria across departments to ensure uniform assessment and management.
- Digital Record Keeping: All inspection records are digitized, enhancing accessibility and simplifying audit and compliance processes.
- Real-Time Updates and Reporting: Update safety glasses status immediately after inspections to facilitate timely actions such as replacements or additional checks.
- Integrated Training Modules: Includes training resources to ensure inspectors are well-versed in safety standards and inspection criteria.
- Customizable Checklists: Tailor inspection checklists to specific industry hazards, ensuring relevant and effective checks.
Benefits of Using SIM
- Enhanced Compliance: Maintains detailed, accessible records for consistent regulatory and internal compliance.
- Increased Safety: Regular, thorough inspections using SIM can significantly reduce the risk of accidents associated with faulty or inadequate eye protection.
- Cost Efficiency: Streamlines PPE maintenance, reducing the need for frequent replacements and potential non-compliance fines.
- Employee Confidence: Demonstrates a commitment to safety, boosting worker confidence in their protective equipment and workplace safety culture.
Conclusion
Incorporating a Safety Inspection Manager into your safety protocols can greatly improve the management of safety glasses inspections, leading to better compliance, enhanced safety, cost savings, and increased employee trust in workplace safety measures.